charpy impact test in abaqus|Modeling and simulation of Charpy impact test of : import Experimental investigations have been carried out to assess the impact . 26 de mai. de 2023 · Ao explorar opções para clonar o Messenger do Facebook, encontramos soluções variadas que se destacam por suas funcionalidades e facilidade de uso. . Depois de colocar o Parallel Space à prova, nossa equipe verificou que este aplicativo é uma excelente opção como aplicativo para clonar o messenger, além de .
{plog:ftitle_list}
Resultado da 89. Rating. Popularity. Terms. Usability. Customer Service. BetonRed was established in 2022 and is gaining popularity in Canada. 85/100 Reviewed .
I am trying to simulate the Charpy test using Abaqus, could someone specify the boundary conditions that should be taken and which model should be followed.
Experimental investigations have been carried out to assess the impact .work presents the finite element modeling and simulation of V-notch Charpy impact .
This work emphasizes the modeling and simulation of Charpy impact test to evaluate fracture energy at different pendulum velocities of armor maraging steel 300 using . Experimental investigations have been carried out to assess the impact strengths of both of these self-healing Al6061 composites using Charpy impact test. Charpy impact test has been simulated using Johnson-cook plastic material model with damage. This video takes you through critical steps such as defining Johnson cook . Charpy Impact Test using Abaqus Explicit. The Johnson-Cook plasticity model with rate-dependency and damage is used for the beam specimen.If you are interest.
In order to determine parameter D 4 by trial algorithm, FE model of the Charpy impact test was developed in the Abaqus/Explicit software. The model consisted of three . This simulation shows the impact testing to calculate the resilience of materials. The Izod testing has been simulated with V-notched sample. A sensitivity study has been . FE models of the Charpy impact test specimens were developed in the ABAQUS Explicit software with the damage model specified through a VUMAT. A half model of the Charpy test specimen and the impactor (hammer) with the z -plane as the plane of symmetry and the z -axis defining the thickness direction was prepared as shown in Fig. 8 for reducing .
UNIVERSAL TENSILE TESTER warehouse
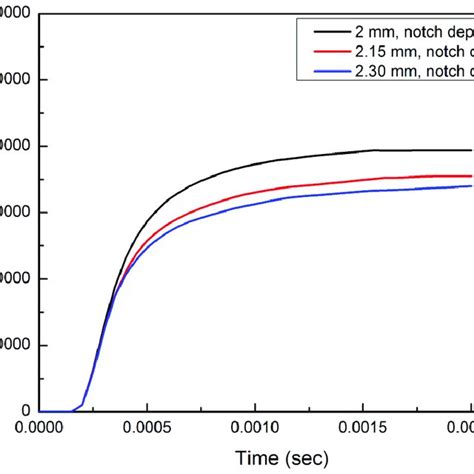
I want to determine the impact energy absorbed by epoxy sample in Izod and Charpy impact test by simulating the impact tests in ANSYS workbench v12. I am having the experimental values for same. View Charpy Impact Test with Abaqus XFEM For related Work contact me on 7891401376. or mail me [email protected] can Join me -Telegram Link - https://t.me/join.
The Charpy impact test is the standard test to determine the fracture toughness of materials and the ductile . Abaqus image of Charpy specimen model meshed with hexagonal finite elements.
Hence in this work, the numerical model of the flatwise Charpy impact test is developed, and a FEA of the impact test is performed in ABAQUS/EXPLICIT. A macroscale approach is followed with laminae material properties determined through RVE analysis of the composite microstructure. . The Charpy impact test is a three-point bending at a . https://drive.google.com/open?id=1641POKJilXuB-jKoV56teFTw81qBjWm-Charpy Impact Testelement deletiondamageoutput request - SDV, STATUS (important!!)obtained by conducting Charpy impact test in Abaqus 6.14. From the numerical analysis the impact energy for the base specimen is 95.33 J and maximum Von Mises Stress is 401.4 Mpa and for weld specimen the impact and stress values are 106.85 J and 405.4 Mpa respectively. The impact energyMaterial impact toughness can be measured by various types of test such as the Charpy V-notch impact test, Izod test or K IC test. The most commonly used test is the Charpy impact test (see Fig. 6.9), which gives an indication of the toughness of a material at a specified temperature.It is not a particularly accurate test but can give a general indication of the ability .
Modeling and simulation of Charpy impact test of maraging steel
The utilization of Finite Element Analysis (FEA) has emerged as a crucial methodology in the field of structural and elasticity analysis, facilitating researchers in their understanding of material responses to diverse thermal or structural loads. This study investigates the utilization of FEA to simulate the Impact characteristics of titanium composites, with .Modeling and simulation of Charpy impact test of maraging steel 300 using Abaqus, D Madhusudhan, Suresh Chand, S Ganesh, U Saibhargavi This simulation shows the impact testing to calculate the resilience of materials. The Izod testing has been simulated with V-notched sample. A sensitivity s.
http://www.universalgripco.com/#!astm-e23/zkr7jA quick strain map video of a Charpy Impact Test performed on an Impact Tester from Universal Grip. The Charpy impact test, also commonly referred to as the Charpy V-notch test by material scientists, serves as a standardized high-strain rate examination to quantify the energy absorbed by a material upon fracture. The absorbed energy functions as an indicator of the material’s notch toughness.hi my friendsto get this tutorial file (CAE 2017 AND INP)contact us email: [email protected]
The case studies considered in the paper are based on previously validated Abaqus studies for the Charpy impact test [18] [19][20], the pressure vessel penetration test [21][22][23], and the .In materials science, the Charpy impact test, also known as the Charpy V-notch test, is a standardized high strain rate test which determines the amount of energy absorbed by a material during fracture.Absorbed energy is a measure of the material's notch toughness.It is widely used in industry, since it is easy to prepare and conduct and results can be obtained quickly and .
The mesh network was selected to simulate the Charpy test as presented in Figure 1b. The size of the sides of the elements is between 0.25 mm and 0.75 mm and the number of nodes and elements for .
DOI: 10.1016/j.ijmecsci.2020.105627 Corpus ID: 216511752; Determination of Johnson–Cook parameters and evaluation of Charpy impact test performance for X80 pipeline steel @article{Cao2020DeterminationOJ, title={Determination of Johnson–Cook parameters and evaluation of Charpy impact test performance for X80 pipeline steel}, author={Yuguang Cao . Charpy impact test has been simulated using J-C constitutive and failure models with the determined parameters. Reasonable agreements between the simulation and experimental results have been achieved. On this basis, the effects of the pendulum velocity, specimen width and striker radius on Charpy impact test results are studied.This work emphasizes the modeling and simulation of Charpy impact test to evaluate fracture energy at different pendulum velocities of armor maraging steel 300 using ABAQUS. To evaluate the fracture energy, V-notch specimen is fractured using the Johnson and Cook Damage model. The Charpy impact tests are of great importance related to fracture properties of steels. The .
Bursting Strength Tester warehouse

The instrumented Charpy impact test is largely applied in industry, due to the fact that it is easy to conduct and results can be obtained quickly and with little cost. However, Charpy impact energy only allows a rather qualitative description of brittleness. . The ABAQUS 5.4 finite element analysis program (implicit time integration in . The Charpy impact test performance was experimentally and numerically studied for two advanced high-strength steel sheets (AHSS) TWIP940 and TRIP590 as well as for a high strength grade 340R. . The new damage model along with the anisotropic yield function Hill1948 was incorporated into the ABAQUS/Explicit FEM code, which performed reasonably .Numerical Modeling of Charpy Impact Test to Determine the Fracture Characteristics of Aluminium Alloy 6061 Salman Pervaiz, Sathish Kannan, Karthikeyan Ram, and Wael A. Samad . The FE model for Charpy test was developed in ABAQUS Explicit. The workpiece materials constitutive behavior was simulated using Johnson – Cook (JC) material model as . The case studies considered in the paper are based on previously validated Abaqus studies for the Charpy impact test [18] [19] [20], the pressure vessel penetration test [21][22][23], and the .
Charpy impact test has been simulated using J-C constitutive and failure models with the determined parameters. Reasonable agreements between the simulation and experimental results have been achieved. On this basis, the effects of the pendulum velocity, specimen width and striker radius on Charpy impact test results are studied.Charpy Impact Testing isn’t just a routine quality control measure—it’s a critical tool for evaluating the resilience of materials in the face of sudden loads. When a sudden force strikes a material, can it withstand the impact without breaking or shattering into pieces? This is precisely what Charpy Impact Testing helps us understand. By simulation using Abaqus software, the Charpy impact test was conducted todetermine the shear lips ratio, energy absorbed, displacement and force. It was found that the V-shape side groove shape .
Modeling and simulation of Charpy impact test of
How to simulate FE analysis of Charpy Impact Test on
Determination of Johnson–Cook parameters and evaluation of
17 de jan. de 2023 · In solving the portfolio optimization problem, the mean-semivariance (MSV) model is more complicated and time-consuming, and their relations are unbalanced because they conflict with each other due to return and risk. Therefore, in order to solve these existing problems, multi-strategy adaptive particle swarm optimization, namely .
charpy impact test in abaqus|Modeling and simulation of Charpy impact test of